About Sheet Metal Fabrication
Sheet metal processing is an important process for forming sheet metal products. Sheet metal manufacturing includes traditional cutting, punching, bending and forming methods and process parameters, as well as various cold stamping die structures and process parameters, various equipment working principles and operating methods, and new stamping technology. Stainless steel sheet metal processing is called sheet metal parts manufacturing.
Youyun Automation mainly provides sheet metal cutting, bending, welding and spraying processes. Different sheet metal parts can be customized for customers to manufacture firmly functional parts, such as panels, brackets and housings, etc.
One of the three main methods of fabricating sheet metal is sheet metal cutting. In this sense, sheet metal fabrication can be thought of as a subtractive manufacturing process (like CNC machining), since usable parts can be made by simply removing parts of material. Fabricators can use a variety of different machines to cut sheet metal.
We mainly use laser cutting. Laser cutting machine is an efficient and high-precision sheet metal processing equipment, which has the following advantages, so it is widely used in sheet metal processing:
1. High cutting precision
The laser cutting machine adopts a high-precision optical system, which can adapt to sheet metal materials of different shapes, sizes and thicknesses. The cutting accuracy is as high as 0.1 mm, which can meet the needs of high-precision sheet metal processing.
2. Fast Cutting Speed
Laser cutting machines use high-power lasers that are able to complete a large number of cutting jobs in a short period of time. For example, the maximum power of a fiber laser cutting machine can reach about 10,000W, and it can cut stainless steel, copper, aluminum and other materials at a speed of several meters per second.
3. Good Cutting Quality
Laser cutting has no physical contact, so it will not leave any marks and deformation on the surface of the cutting material, and the cutting-edge quality is good, the finish is high, and there are no burrs, which meets the needs of high-quality parts.
4. Wide Application
Laser cutting machine can cut a variety of sheet metal materials, such as stainless steel, aluminum plate, copper plate, alloy steel, carbon steel, etc. Using lasers of different powers, sheet metal materials of different thicknesses can be cut.
5. High Efficiency and Energy Saving
The laser cutting machine adopts high-efficiency photoelectric conversion technology, and the power conversion rate is as high as 30%-40%, which saves about 30%-40% of electricity compared with traditional mechanical processing equipment.
To sum up, the application of laser cutting machine in sheet metal processing is quite extensive, and its advantages such as high precision, high efficiency, high quality and applicability make it an indispensable processing tool in many industries.
Another major category of sheet metal fabrication processes is sheet metal bending.
Sheet metal bending processing (Sheet Metal Bending), the bending and forming of metal sheets are carried out on the bending machine, the workpiece to be formed is placed on the bending machine, the brake shoe is lifted by the lifting lever, and the workpiece slides to the appropriate position. position, then lower the brake shoe onto the workpiece to be formed, and the metal is bent and formed by applying force to the bending lever on the bending machine.
The minimum bend radius is a function of the ductility and thickness of the metal being formed. For aluminum sheets, the bending radius of the metal is greater than the thickness of the sheet. When bending, due to a certain amount of rebound, the bending angle of the metal is slightly larger than the required angle.
After sheet metal has been cut and bent, it can be joined together by welding. The welding method is spot welding, argon arc welding, gas shielded welding, solder welding, etc. Different materials need to be used in different ways.
About Sheet Metal Parts Spraying
After welding, the surface of the product can be treated according to customer requirements and sprayed into different colors.
Material Selection
The materials generally used in sheet metal processing are cold-rolled sheet (SPCC), hot-rolled sheet (SHCC), galvanized sheet (SECC, SGCC), copper (CU) brass, red copper, beryllium copper, aluminum sheet (6061, 5052, 1010, 1060, 6063, duralumin, etc.), stainless steel (mirror surface, brushed surface, matte surface), depending on the function of the product, the selection of materials is different, generally it is necessary to consider the use and cost of the product.
- Cold-rolled sheet SPCC, mainly used for electroplating and baking varnish, low cost, easy to form, material thickness ≤ 3.2mm.
- Hot-rolled sheet SHCC, material T≥3.0mm, also use electroplating, baking varnish parts, low cost, but difficult to shape, mainly use flat parts.
- Galvanized sheet SECC, SGCC. SECC electrolytic plates are divided into N material and P material. N material is mainly not used for surface treatment, which has high cost, and P material is used for sprayed parts.
- Copper: It is mainly used as a conductive material, and its surface treatment is nickel plating, chrome plating, or no treatment, and the cost is high.
- Aluminum plate; generally, use surface chromate (J11-A), oxidation (conductive oxidation, chemical oxidation), high cost, silver plating, nickel plating.
- Aluminum profiles; materials with complex cross-sectional structures, which are widely used in various sub-boxes. The surface treatment is the same as that of the aluminum plate.
- Stainless steel; mainly used without any surface treatment, high cost.
After We Accept The Project
Preliminary test of sheet metal products, trial production of product processing and mass production of products. In the process of product processing and trial production, we communicate with customers in a timely manner, and after obtaining the evaluation of the corresponding processing, we proceed to mass production of products.
Drawing Review:
To write the process flow of a part, one must first know the various technical requirements of the part drawing; then the review of the drawing is the most important part of the process flow of the part.
- Check that the drawing is complete.
- The drawing view relationship, whether the labeling is clear and complete, and the dimension unit is marked.
- Assembly relationship, key dimensions of assembly requirements.
- The difference between the old and new versions.
- Translation of pictures in foreign languages.
- Code conversion at the table.
- Feedback and resolution of drawing problems.
- Material.
- Quality requirements and process requirements.
- Officially issued drawings must be affixed with a quality control seal.
Other Posts
What are the application areas of sheet metal casings?
The wide application of sheet metal casings is due to its lightweight, high strength, easy processing and other characteristics, which can meet the needs of
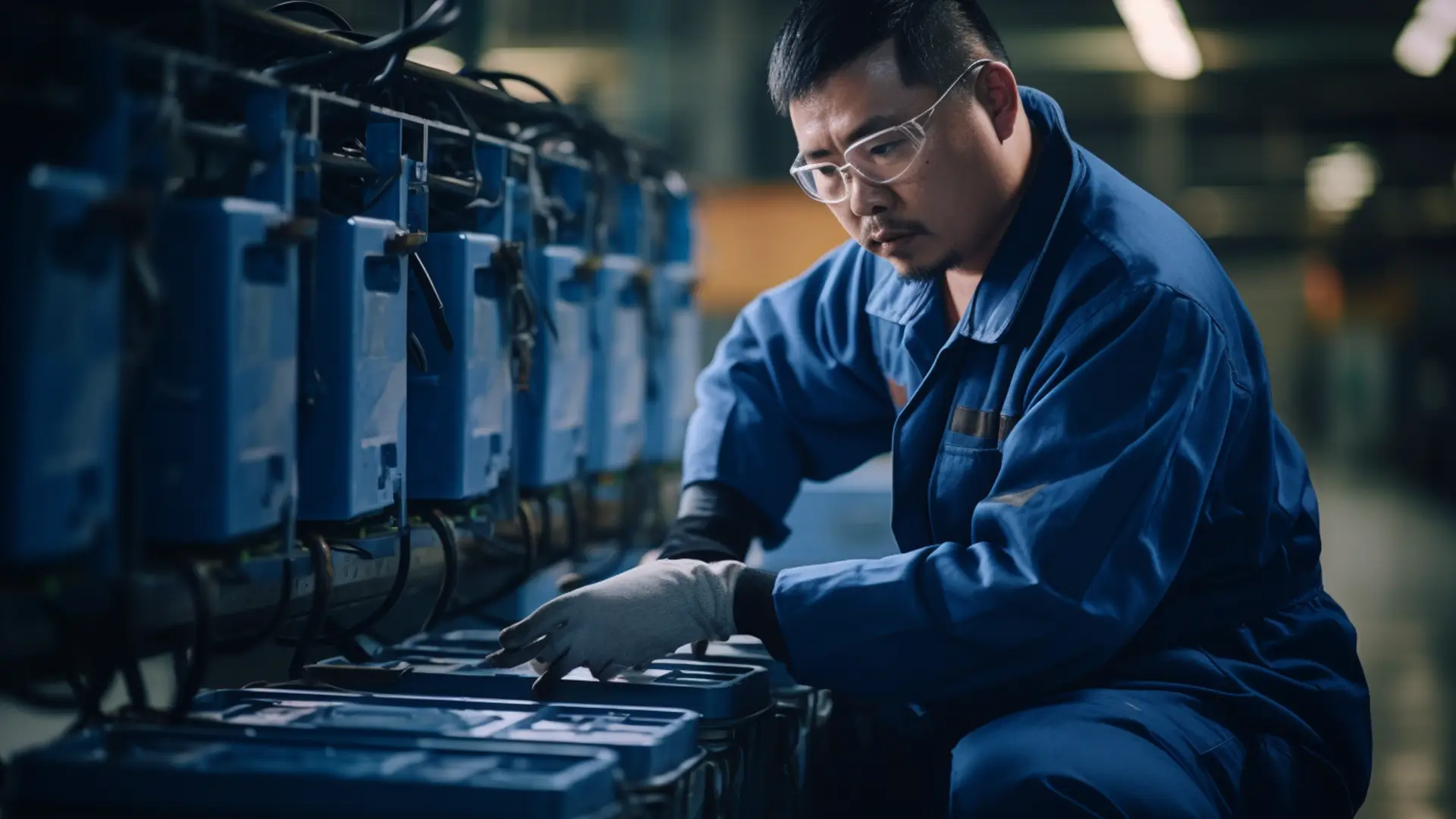
Analysis of current situation and prospects of China’s energy storage battery industry in 2023
Home Analysis of current situation and prospects of China’s energy storage battery industry in 2023 In the composition of the energy storage system, the battery
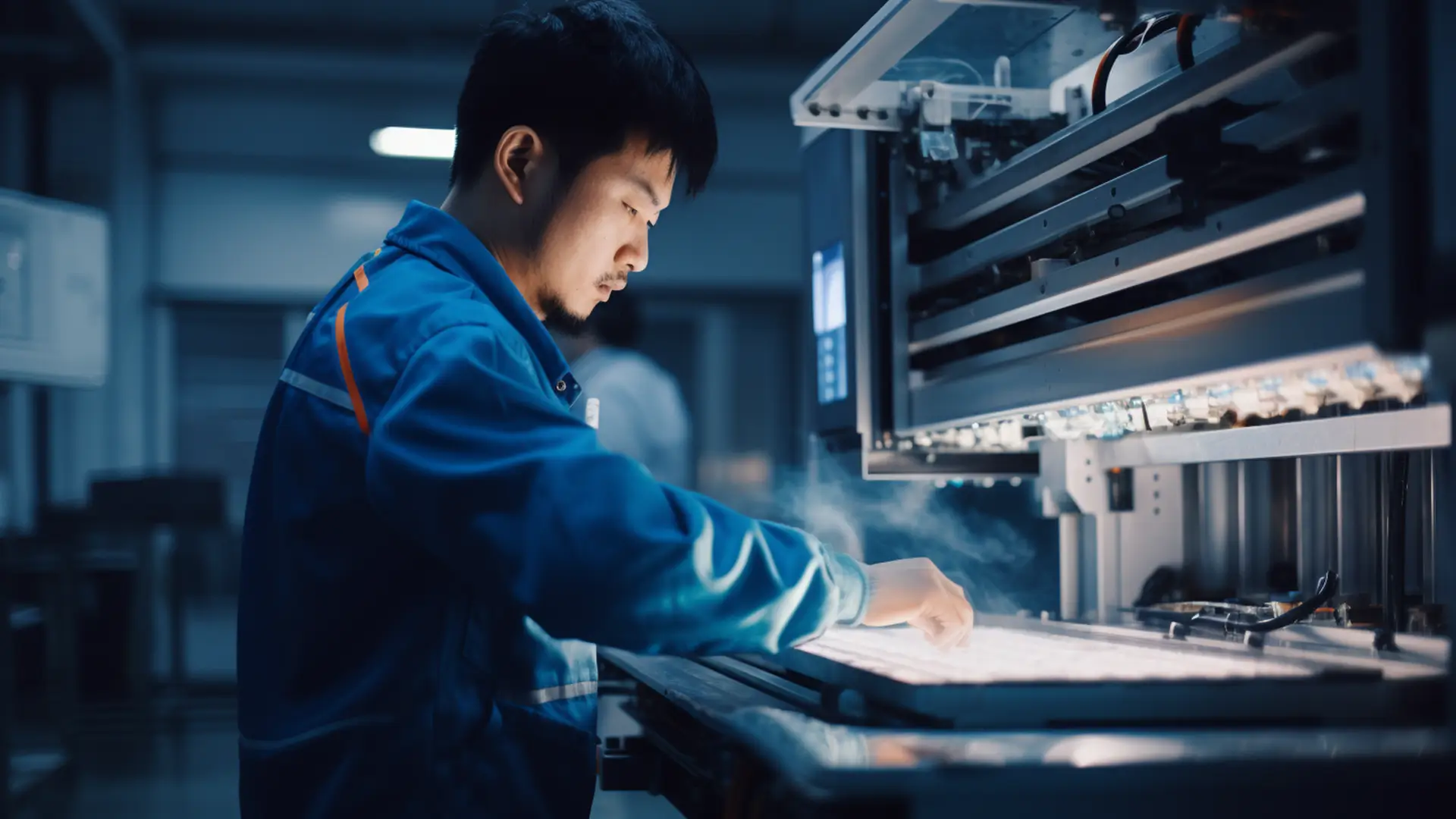
Industrial 3D Printer
Home Industrial 3D Printer 3D printers have been widely used in various fields, bringing great convenience to people’s lives and work. Some of these 3D